Understanding Plastic Injection Molds: A Comprehensive Guide for Businesses
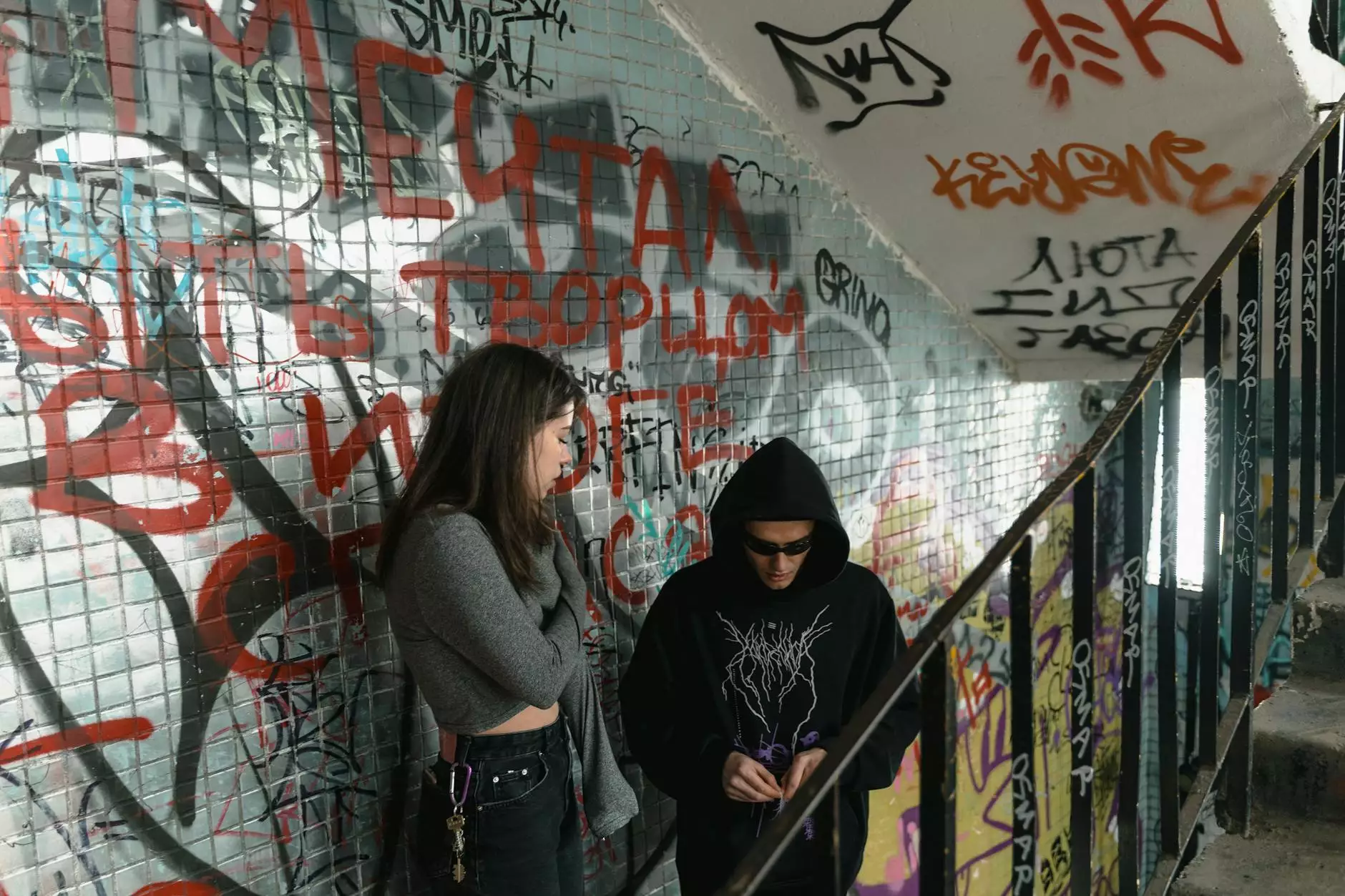
Plastic injection molds represent a pivotal part of modern manufacturing, facilitating the production of high-precision plastic parts across various industries. Their significance cannot be overstated as they contribute to the efficiency, quality, and cost-effectiveness of the manufacturing process. In this article, we will dive deep into the world of plastic injection molds and explore their advantages, applications, and the future trends shaping this industry.
What are Plastic Injection Molds?
Plastic injection molds are specialized tools used in the plastic injection molding process, where molten plastic is injected into a mold cavity to shape it into a desired form. This method is widely appreciated for its ability to produce large quantities of parts with consistent quality and minimal waste.
Components of Plastic Injection Molds
A typical plastic injection mold consists of several essential components:
- Mold Base: The foundation of the mold that holds all parts together.
- Cavity and Core: The two halves of the mold that shape the plastic. The cavity is the outer shape, while the core forms the inner structure.
- Ejector Pins: Mechanisms that push the molded part out of the mold once cooled.
- Cooling Channels: Channels within the mold that allow coolant to regulate the temperature during production.
- Gate System: The entry point through which molten plastic enters the mold cavity.
The Process of Plastic Injection Molding
The plastic injection molding process can be broken down into a series of steps:
- Mold Preparation: Ensuring the mold is clean and ready for use.
- Material Feeding: Plastic pellets are fed into a heated barrel where they are melted down.
- Injection: The molten plastic is injected into the mold under high pressure.
- Cooling: The plastic is allowed to cool and solidify in the mold.
- Ejection: Once cooled, the mold opens and ejector pins push the finished product out.
Benefits of Using Plastic Injection Molds
The advantages of plastic injection molds are numerous, making them a staple in the manufacturing world:
- High Efficiency: Capable of producing thousands of identical parts quickly.
- Cost-Effectiveness: Reduces labor and material costs, particularly for large production runs.
- Precision: Creates intricate parts with a high degree of accuracy.
- Material Versatility: Compatible with a wide range of plastics, allowing for varied applications.
- Reduced Waste: Minimizes scrap material through effective design parameters.
Applications of Plastic Injection Molds
Plastic injection molds are utilized in various industries, showcasing their versatility:
1. Automotive Industry
In the automotive sector, plastic injection molds are used to create dashboards, panels, and various components that require high durability and precision.
2. Consumer Goods
Everyday products such as containers, toys, and electronics cases are mass-produced using injection molding, allowing for creative designs and functional packaging.
3. Medical Devices
The medical industry relies on injection-molded components for devices that require stringent safety and hygiene standards, such as syringes, surgical tools, and housings for electronics.
4. Industrial Applications
Many industrial components, including gears, housings, and brackets, are manufactured using injection molding due to its ability to maintain mechanical strength and tolerance levels.
Choosing the Right Plastic Injection Mold Manufacturer
Selecting the right manufacturer for plastic injection molds is crucial to ensure quality and reliability. Here are some considerations:
- Experience: Look for manufacturers with a proven track record in producing high-quality molds.
- Technology: Ensure they utilize advanced technologies in mold design and manufacturing.
- Quality Control: Investigate their quality assurance processes and certifications.
- Customer Service: Choose a partner that offers strong support throughout the project lifecycle.
DeepMould: Leading the Way in Plastic Injection Molding Solutions
At DeepMould.net, we specialize in providing top-notch plastic injection molds for a variety of industries. Our commitment to excellence is manifested in our cutting-edge technology, expert team, and rigorous quality control processes. We take pride in meeting our clients’ diverse manufacturing needs, ensuring that every project is completed to the highest standards.
Our Services Include:
- Custom Mold Design: Tailored molds designed to meet specific requirements and specifications.
- Prototyping: Rapid prototyping services to help customers validate their designs before full-scale production.
- Mold Maintenance: Comprehensive maintenance and repair services to prolong mold life and performance.
- Production Support: Ongoing support throughout the production process, from initial mold creation to final product delivery.
The Future of Plastic Injection Molding
The landscape of plastic injection molds is continuously evolving with advancements in technology and shifts in market demands. Here are some trends to watch:
- Automation: Increased use of robotics in the injection molding process for improved efficiency and precision.
- Sustainability: A growing focus on eco-friendly materials and recycling processes in mold production.
- 3D Printing Integration: Merging traditional molding with 3D printing to streamline mold design and prototype creation.
- Smart Manufacturing: Adoption of the Internet of Things (IoT) for real-time monitoring and optimization of the injection molding process.
Conclusion
In summary, plastic injection molds are an essential aspect of modern manufacturing, offering unparalleled efficiency, precision, and cost-effectiveness. Businesses looking to thrive in competitive landscapes should consider partnering with experienced manufacturers like DeepMould.net. By harnessing the benefits of plastic injection molding, organizations can innovate, scale operations, and meet customer demands with exceptional quality and speed.
For inquiries regarding our services, please visit DeepMould.net and discover how we can assist you in your manufacturing journey.