The Pinnacle of Manufacturing: The Essential Role of Precision Molds
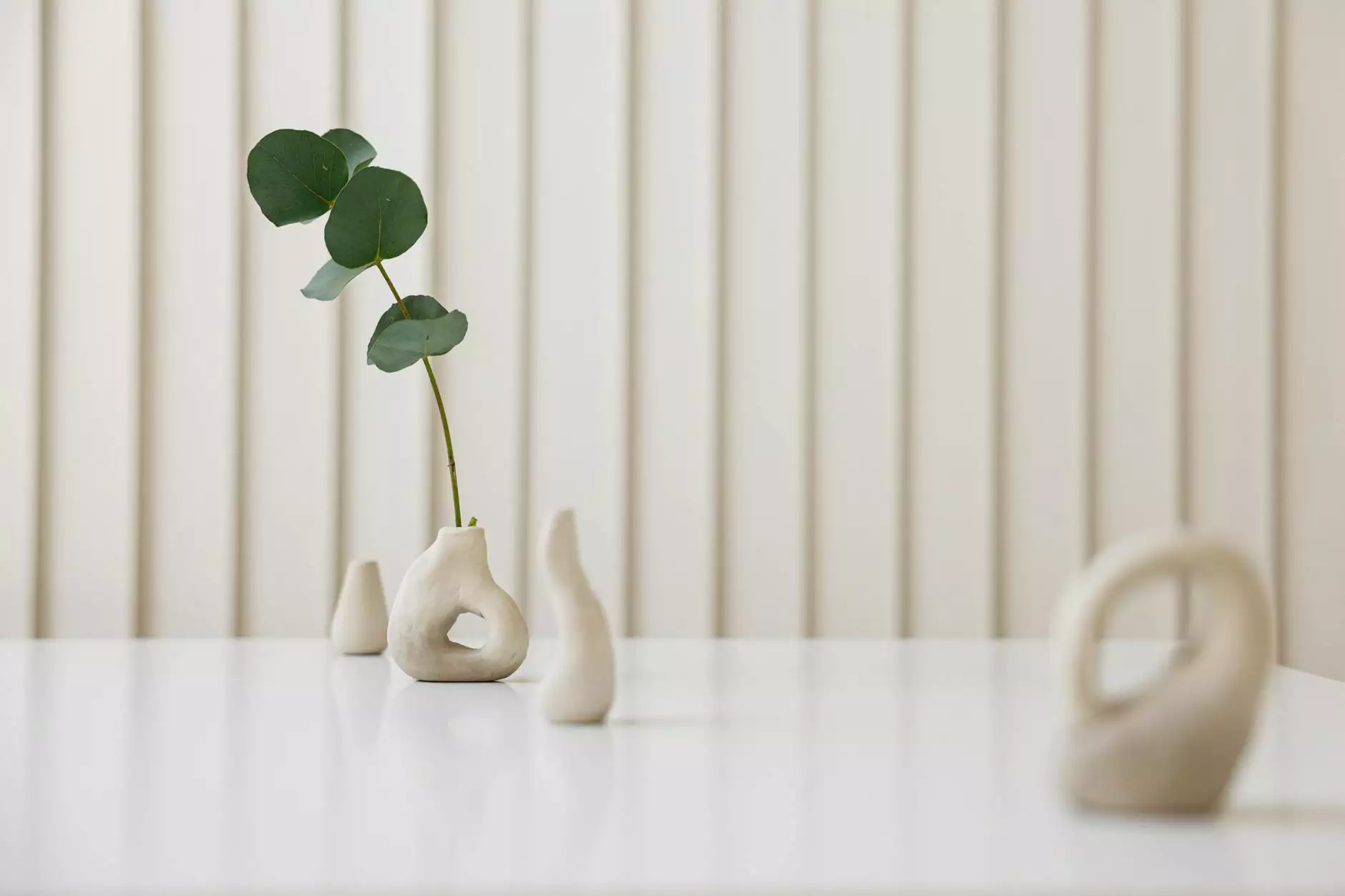
Introduction to Precision Molds
In the realm of manufacturing, the term precision molds refers to highly accurate and specially designed tools used to shape materials into predefined patterns. The demand for these molds has surged, driven by the need for high-quality products that meet exact specifications. This article delves deeply into the significance of precision molds within the metal fabrication industry and elucidates how they contribute to delivering superior products.
What Are Precision Molds?
At its core, a precision mold is an intricate tool composed of various components that work together to form products from materials such as plastics, metals, and composites. They are essential in processes such as injection molding, blow molding, and compression molding. The precision aspect highlights the exactness with which these molds are manufactured, allowing them to produce consistent and high-quality outputs.
Key Characteristics of Precision Molds
- High Tolerance Levels: Precision molds can achieve tight tolerances, often within thousandths of an inch.
- Durability: Made from robust materials, precision molds are designed to withstand rigorous manufacturing conditions.
- Complex Designs: Capable of producing intricate shapes and features that conventional molds cannot.
- Efficiency: Streamlined production processes that minimize waste and maximize output quality.
The Importance of Precision Molds in Metal Fabrication
In the metal fabrication sector, the significance of precision molds cannot be overstated. They play a critical role in determining the quality of the final product while also impacting the production process itself.
Enhancing Product Quality
The use of precision molds ensures that every manufactured item meets the desired specifications and quality standards. This is pivotal in industries such as automotive, aerospace, and consumer electronics, where deviations can lead to significant malfunctions or safety hazards. By utilizing precision molds, companies can achieve:
- Consistent Dimensions: Maintaining the same size and shape across all products.
- Improved Finish: Delivering superior surface finishes that enhance the aesthetic and functional aspects of products.
- Reduced Rework: Minimizing the need for corrections and adjustments post-manufacturing.
Promoting Manufacturing Efficiency
Efficiency in production is tantamount to profitability. Precision molds contribute to this efficiency through:
- Faster Cycle Times: Precision molds are designed to streamline production time, allowing manufacturers to produce more items in less time.
- Lower Material Waste: Reducing scrap materials as molds are designed for exact fits.
- Interchangeability: Being able to replace one mold with another quickly, reducing downtime between different production runs.
Casting Techniques Utilizing Precision Molds
Various casting techniques leverage the capabilities of precision molds in metal fabrication. Let's explore some of the most popular techniques:
Injection Molding
Injection molding is a widely used method for producing a variety of parts. In this process, molten material is injected into the mold under high pressure, allowing for quick production and the ability to create complex shapes. The precision of the molds ensures that each item is consistent in quality.
Die Casting
Die casting involves forcing molten metal into a mold cavity under high pressure. This technique is ideal for mass production of small to medium-sized parts with intricate designs. The precision molds used in die casting enable manufacturers to produce components that meet tight tolerances.
Blow Molding
Blow molding is predominantly used for creating hollow plastic parts. The precision molds involved in this process play a significant role in achieving seamless, uniform products, such as bottles and containers.
The Evolution of Precision Molds
The evolution of precision molds has paralleled advancements in technology. Traditionally, mold-making involved manual labor and basic machinery. However, innovations such as Computer Numerical Control (CNC) machining and 3D printing have dramatically revolutionized the design and production of molds.
Technological Advancements
The integration of advanced technologies into mold-making processes has brought about several improvements:
- Increased Design Capabilities: Complex geometries can now be designed and fabricated with ease.
- Speed: Rapid prototyping technologies facilitate quick mold testing and adjustments.
- Cost Reduction: Enhanced efficiency and reduced waste translate to lower production costs.
Choosing the Right Precision Mold for Your Business
Selecting the appropriate precision mold is crucial for any business involved in manufacturing. Here are some factors to consider when making this decision:
Material Selection
The choice of material for both the mold and the final product affects durability, performance, and cost. Factors such as thermal properties, corrosion resistance, and mechanical strength should be assessed.
Mold Design and Complexity
The design of the mold must accommodate the specifics of the product being manufactured. Complex designs may require specialized molds that can handle intricate features without compromising on quality.
Production Volume and Lifecycle
Consideration of the expected production volume is essential. High-volume production may justify a higher initial investment in more durable molds, whereas lower volumes may benefit from cost-effective options.
Future Trends in Precision Mold Technology
The future of precision molds looks promising, driven by constant advancements in technology and manufacturing processes. Key trends include:
Automation and Smart Molding Solutions
Automation is set to enhance the efficiency and precision of mold production. Smart technology, including IoT-enabled devices, will allow for real-time monitoring and adjustments during the manufacturing cycle.
Sustainability Initiatives
As industries increasingly focus on sustainability, precision molds are expected to evolve with eco-friendly materials and processes that reduce environmental impact.
Conclusion
In conclusion, precision molds are indispensable tools in the metal fabrication industry, enabling manufacturers to achieve high-quality products efficiently. As technology continues to advance, the capabilities and applications of these molds will expand, further solidifying their role in modern manufacturing. Companies like Deep Mould are at the forefront of this evolution, setting the standard for quality and precision in mold design and production. Embracing these advancements can lead businesses toward greater success in an increasingly competitive market.
Contact Us
If you are looking for top-quality precision molds tailored to your specific manufacturing needs, consider partnering with Deep Mould. Our experienced team is dedicated to delivering innovative solutions that will help you achieve your production goals.