Unlocking Potential: The Power of Precision Plastic Parts
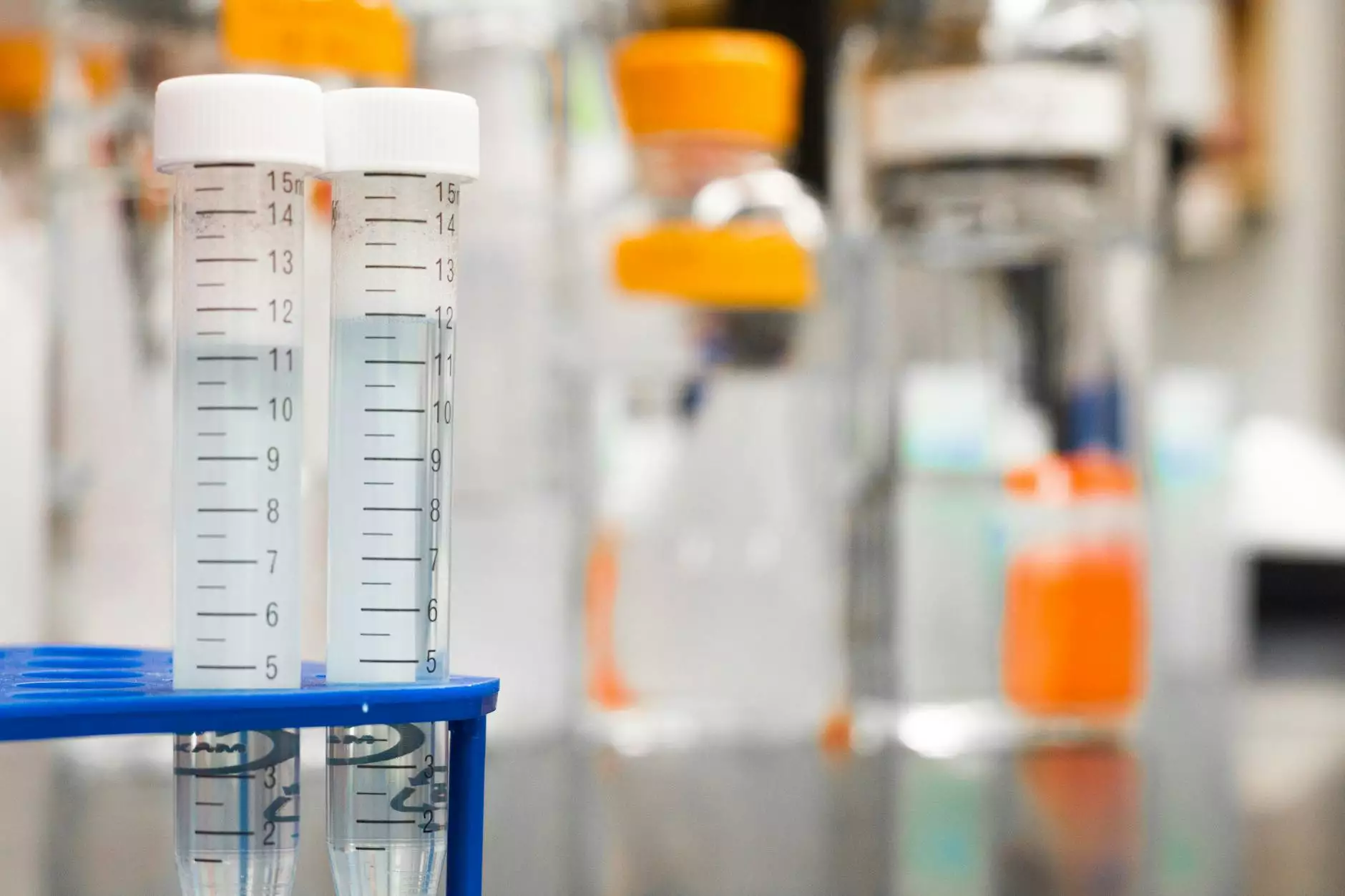
Precision plastic parts have become an indispensable aspect of modern manufacturing, impacting various sectors from automotive to medical devices. As businesses seek to innovate and optimize, understanding the role and capabilities of precision plastic components is essential. This article will delve into the intricacies of precision plastic parts, including their manufacturing processes, advantages, applications, and future trends.
Understanding Precision Plastic Parts
At its core, precision plastic parts are components manufactured with high accuracy and specificity, tailored to meet strict tolerances and functionality. These parts are created using advanced techniques that ensure uniformity, reduced waste, and durability. The significance of precision lies in its broad applicability, enabling manufacturers to cater to high-demand sectors where performance and reliability are paramount.
The Importance of Precision in Manufacturing
In an era where competition is fierce, the need for precision cannot be overstated. Here are several reasons why precision is critical in manufacturing plastic parts:
- Quality Assurance: Precision guarantees that parts meet the required specifications, leading to enhanced product quality.
- Cost Efficiency: Minimizing waste during production through precision reduces overhead costs and enhances profitability.
- Performance Optimization: Parts that fit perfectly function better, reducing the risk of failure in critical applications.
Manufacturing Processes for Precision Plastic Parts
Several manufacturing processes contribute to the creation of precision plastic parts, each with its own set of advantages, depending on the application requirements. Below, we explore some of the most common methods:
Injection Molding
Injection molding is a predominant technique for producing precision plastic parts. In this method, plastic resin is heated until it reaches a molten state and is then injected into a mold. This allows for:
- High Volume Production: Ideal for manufacturing large quantities of identical parts.
- Complex Geometries: Capable of producing intricate shapes that meet precise specifications.
- Material Versatility: Allows for a variety of plastics to be used, each tailored to specific performance criteria.
3D Printing
3D printing, also known as additive manufacturing, is gaining traction in producing precision plastic parts. This method builds parts layer by layer, allowing for unparalleled design flexibility. Benefits of 3D printing include:
- Rapid Prototyping: Quickly turn designs into physical parts for testing and validation.
- Customization: Ideal for creating bespoke parts tailored to specific customer needs.
- Reduced Lead Times: Streamlines the production process, often leading to faster delivery times.
Thermoforming
Thermoforming is another process used for creating plastic parts, particularly in applications requiring large sheets of plastic. This method involves heating plastic sheets until pliable and then forming them over molds. Notable advantages include:
- High Efficiency: Suitable for large-scale production of relatively simple shapes.
- Cost-Effectiveness: Lower tooling costs compared to injection molding.
- Material Waste Reduction: Offers a more efficient use of materials in certain applications.
Applications of Precision Plastic Parts
The applications of precision plastic parts span numerous industries, highlighting their versatility and importance. Key sectors include:
Automotive Industry
In the automotive sector, precision plastic parts play a crucial role in:
- Interior Components: From dashboards to seat frames, precision ensures safety and comfort.
- Exterior Detailing: Headlight housings and bumpers often require precise molding for optimized aerodynamics and aesthetics.
- Under-the-Hood Applications: Engine components benefit from lightweight plastic parts designed to withstand high temperatures.
Medical Field
The medical industry relies heavily on precision plastic parts for:
- Devices and Equipment: Surgical tools and diagnostic equipment must meet stringent accuracy standards.
- Disposable Items: Syringes and IV bags require precision for safety and effectiveness.
- Patient-Specific Solutions: 3D printing enables tailored prosthetics and implants.
Consumer Electronics
In the realm of consumer electronics, precision parts facilitate:
- Enclosures: Protecting delicate components in phones, tablets, and computers.
- Connectors and Interfaces: Ensuring compatibility and performance between devices.
- Internal Components: Circuit boards and other internal parts must maintain precision for functionality.
The Benefits of Precision Plastic Parts
The advantages of incorporating precision plastic parts into manufacturing processes are profound and multifaceted:
Durability and Longevity
Precision-engineered plastic parts often exhibit superior durability, meaning they can withstand stress, heat, and environmental factors better than standard parts.
Weight Reduction
Using precision plastics can significantly reduce product weight, which is especially beneficial in industries like automotive and aerospace, where weight savings translate directly to increased efficiency and reduced fuel costs.
Enhanced Aesthetics
Precision parts allow for a high level of detail and finish, improving the overall look of the final product, which is crucial in consumer-centric industries.
Environmental Considerations
As companies prioritize sustainability, precision plastic parts made from recyclable materials can help minimize environmental impact, making them a forward-thinking choice for modern manufacturers.
Future Trends in Precision Plastic Parts
The landscape of manufacturing is continuously evolving, and precision plastic parts are at the forefront of this change. Emerging trends include:
Increased Automation
Advanced automation technologies are being integrated into manufacturing processes, enhancing precision and consistency while reducing production times and labor costs.
Smart Materials
Innovations in smart materials that respond to environmental changes are opening new avenues for precision plastic components, particularly in areas like safety and performance.
Industry 4.0
The integration of IoT (Internet of Things) in manufacturing processes is revolutionizing the production of precision plastic parts by enabling real-time monitoring and adjustments, leading to greater efficiency and reduced waste.
Conclusion
As industries continue to innovate and strive for excellence, the importance of precision plastic parts will only grow. Their applications, from automotive to medical, underscore their versatility and indispensable role in modern manufacturing. Businesses looking to stay competitive must recognize the transformative potential of precision in their products. By investing in precision manufacturing processes and leveraging the benefits these components provide, companies can enhance their operational efficiency, product quality, and customer satisfaction.
At DeepMould, we understand the significance of precision in your products. Our expertise as metal fabricators positions us to support your journey toward manufacturing excellence. Together, let's embrace the future of precision plastic parts and unlock new opportunities for innovation.