The Art of Plastic Molding: Revolutionizing Metal Fabrication
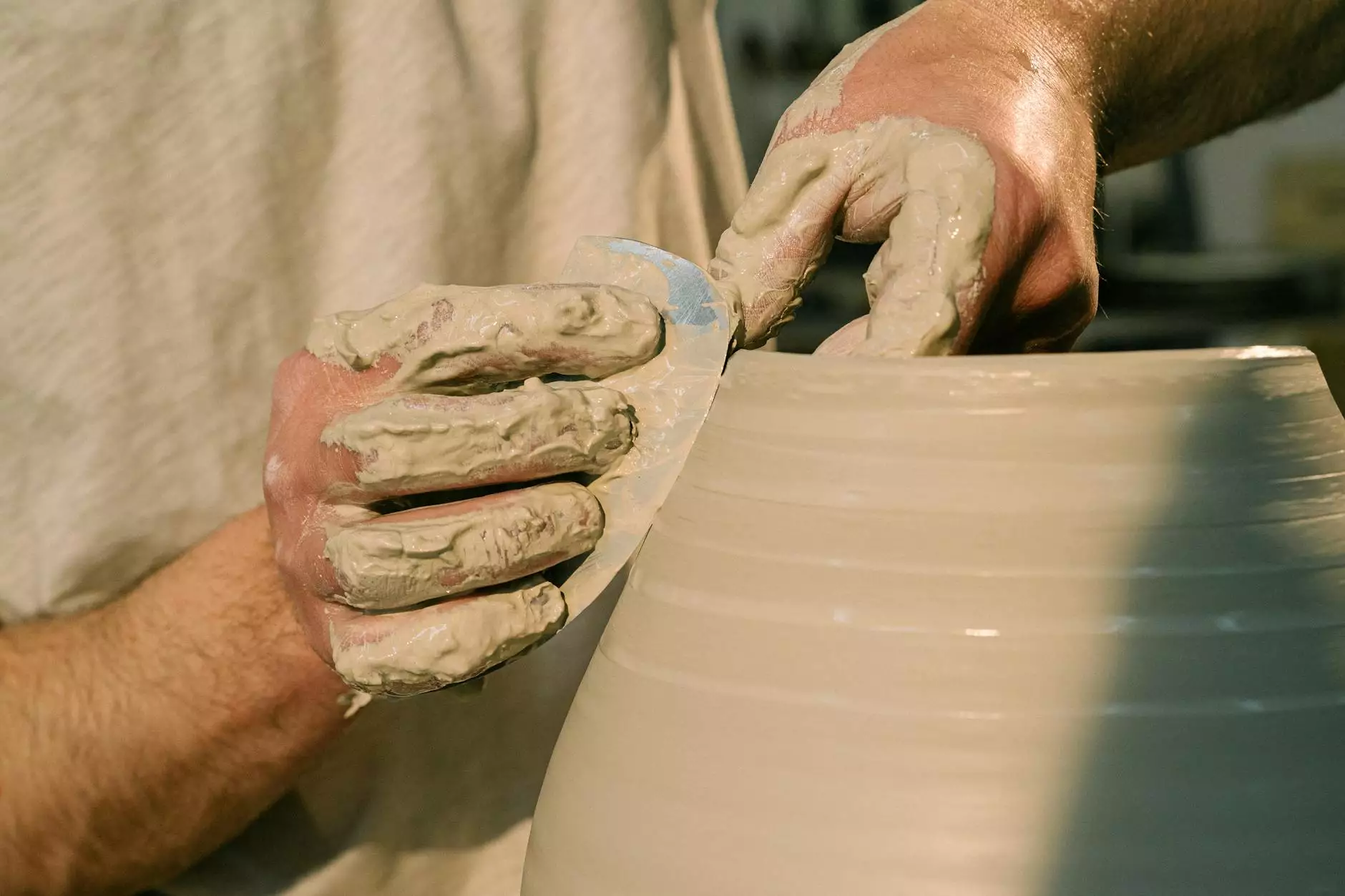
Plastic molding has been a game changer in various industrial sectors, particularly in the field of metal fabrication. As businesses continue to search for innovative solutions to enhance production efficiency, the role of plastic molding cannot be overstated. It represents a dynamic intersection of technology, design, and functionality that empowers manufacturers to create high-quality products with exceptional precision.
Understanding Plastic Molding
Before diving into how plastic molding integrates into metal fabrication, it is essential to grasp the fundamentals of the process. Plastic molding is a manufacturing process that involves shaping plastic materials using a mold. The basic principle is simple: molten plastic is injected into a mold where it cools and solidifies, taking the shape of the mold cavity.
Types of Plastic Molding Processes
There are several types of plastic molding processes, each offering unique advantages:
- Injection Molding: This process involves injecting molten plastic into a mold under high pressure. It allows for high-volume production and complex designs.
- Blow Molding: Used primarily for producing hollow plastic parts, this method forms items like bottles by inflating heated plastic within a mold.
- Compression Molding: Involves placing a measured amount of plastic into an open mold, which is then closed under heat and pressure. This is ideal for large parts.
- Rotational Molding: A versatile process used for creating large, hollow products; plastic is heated in a mold that is rotated, distributing the material evenly.
The Importance of Plastic Molding in Metal Fabrication
The integration of plastic siding in metal fabrication has opened new avenues for innovation. While metal remains a critical material in construction and manufacturing, the incorporation of plastic components has improved versatility and adaptability in product design. Here are some significant benefits:
1. Cost-Effectiveness
Using plastic molding in conjunction with metal fabrication can lead to substantial cost savings. Plastic components generally require less material input and lower processing costs compared to metals. This synergy allows companies to offer competitive pricing while maintaining quality.
2. Design Flexibility
One of the greatest advantages of plastic molding is its design flexibility. Complex shapes and intricate details can be easily achieved that would be challenging with traditional metal fabrication methods. This flexibility allows manufacturers to create custom solutions tailored to specific needs.
3. Weight Reduction
Plastic parts significantly reduce the overall weight of finished products. This is particularly valuable in industries such as automotive and aerospace, where minimizing weight translates to better fuel efficiency and performance. By integrating plastic molding into metal structures, manufacturers can optimize their designs without compromising strength.
4. Enhanced Safety and Durability
By incorporating plastic parts, the overall safety of products can also improve. Plastics can provide insulation from electrical currents and resist corrosion, thereby extending the longevity and durability of metal assemblies. The combination of plastic molding with metal enhances the overall resilience of the product, providing added peace of mind for users.
Applications of Plastic Molding in Metal Fabrication
Plastic molding finds extensive application within the domain of metal fabrication. Here are some exciting examples:
1. Automotive Industry
In the automotive sector, plastic molding is utilized to produce a myriad of components, including dashboards, interior panels, and under-the-hood parts. The lightweight nature of plastic helps improve fuel efficiency while providing aesthetic options that appeal to consumers.
2. Electronics
Many electronic devices integrate both metal and plastic components. Plastic molding helps create housings and internal structures that protect sensitive electronics from environmental factors while also offering design coherence and branding opportunities.
3. Medical Devices
The medical industry benefits greatly from the nuances of plastic molding. Devices like syringes, surgical tools, and casings often combine both metal for functionality and plastic for safety and hygiene. This combination facilitates the production of reliable and sterile medical instruments.
4. Consumer Goods
From kitchen appliances to household items, consumer goods often rely on the marriage of plastic molding and metal fabrication. This synergy allows for products that are both aesthetically pleasing and functional, catering to modern consumer demands.
Choosing the Right Partner: Why DeepMould.net Stands Out
When it comes to embarking on a project that requires expertise in plastic molding and metal fabrication, choosing the right partner is crucial. DeepMould.net stands at the forefront of this industry for several reasons:
1. Experience and Expertise
With years of experience in the industry, DeepMould.net understands the intricacies of both plastic molding and metal fabrication. Their skilled engineers and technicians can offer tailored solutions to meet unique project needs.
2. State-of-the-Art Technology
In the world of manufacturing, staying ahead of technology is crucial. DeepMould.net is equipped with the latest machinery and software, ensuring precision and efficiency in every project. Their advanced capabilities allow for quicker turnaround times without compromising on quality.
3. Commitment to Quality
Quality assurance is a cornerstone of DeepMould.net's operation. By adhering to stringent quality standards, they ensure that all products meet or exceed client expectations. Their commitment to excellence has earned them a reputation as a reliable partner in the industry.
4. Customer-Centric Approach
DeepMould.net prides itself on its customer-centric approach. They collaborate closely with clients from the initial design phase through to the final production, ensuring that every detail is aligned with the client's vision.
Future Trends in Plastic Molding and Metal Fabrication
The future of plastic molding and metal fabrication looks bright, with several trends on the horizon that promise to drive further innovation:
1. Sustainability
As the global focus shifts toward sustainability, manufacturers are exploring environmentally friendly materials and processes. Biodegradable plastics and recycled materials are gaining traction, allowing for eco-conscious production while maintaining the beneficial attributes of plastic molding.
2. Automation and Smart Manufacturing
Automation is becoming increasingly prominent in the manufacturing sector. The integration of smart technology and robotics in plastic molding processes is on the rise, allowing for improved consistency, faster production times, and reduced labor costs. DeepMould.net is at the forefront of this transformation, leveraging technology to enhance their manufacturing processes.
3. Customization
With the rise of consumer demand for personalized products, customization will continue to trend in the plastic molding space. The melding of advanced manufacturing techniques with client-specific requirements enhances the ability to fulfill this demand while ensuring that customization remains cost-effective.
4. Innovations in Material Science
Advancements in material science will provide manufacturers with more options for plastic and composite materials, allowing for enhanced functionality, performance, and durability in products. This will undoubtedly push the boundaries of what can be achieved through plastic molding.
Conclusion
In conclusion, the interplay between plastic molding and metal fabrication is reshaping the future of manufacturing. With its unparalleled benefits in cost-effectiveness, design flexibility, and durability, plastic molding holds a pivotal role in modern production processes. As businesses like DeepMould.net continue to innovate and lead in this field, the potential for growth and advancement remains boundless. Embracing these advancements will position your business at the cutting edge of the industry, ready to meet the challenges and demands of tomorrow.